昨今半導体は日本だけでなく、世界中で不足が拡大しているため、あらゆる電気を使う製品の中でつかわれる非常に需要なパーツの一部となっています。一般に半導体はウェハと言われる円形にプリントされたものを四角に切り出してチップとして使います。
今回は、そのチップを製造する過程で、工程間を搬送するため、あるいは実装(搭載)するときに必要な「コレット」という半導体製造器具についての話題です。
機械は使っていくとそれに装着されている周辺機器なども、次第に摩耗したり、破損したりしていくものです。
半導体で使われるコレットってそもそも何?
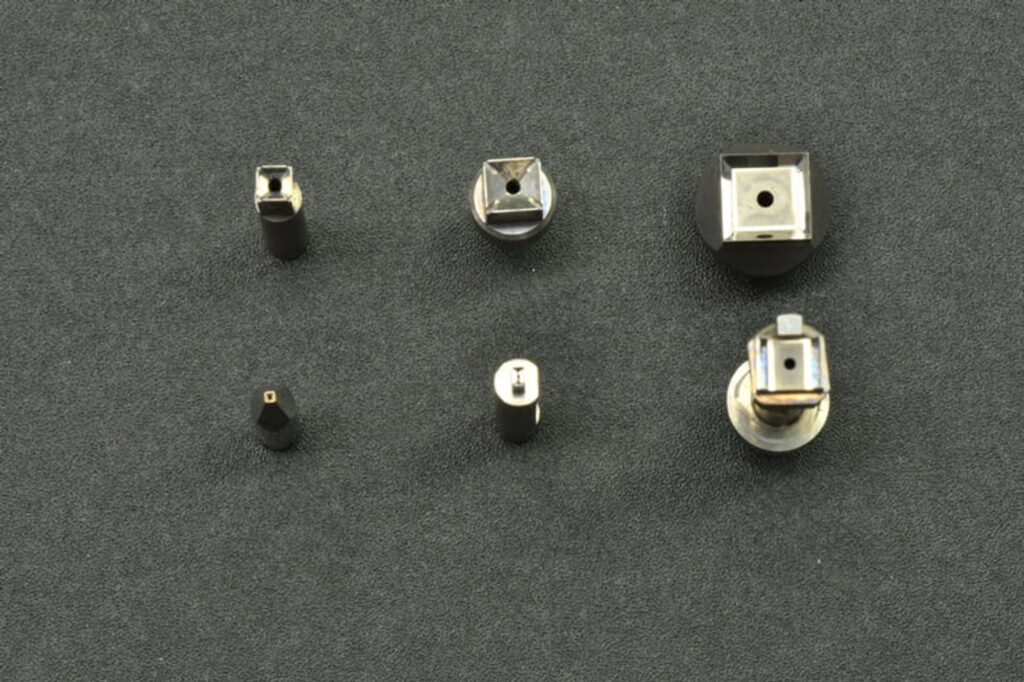
コレットは写真のような器具で、これを半導体製造器具の先端に取り付けて使います。
主に、半導体の搬送に使われます。弊社では先端がとがったものや幅の広いもの、オーダーメイド形式など多数の形状のコレットの作成が可能です。写真は金属ですが、プラスチック、ゴム、セラミックまたそれらの混合で作られます。
半導体製造過程でよく課題として、搬送がそもそもうまくいかなかったり、搬送中に半導体チップにキズがついてしまったり、へこんでしまったりすることが挙げられます。これらをなくし、生産効率を最大限に上げ、良質な製品を生み出すことが求められています。
引っかきキズや凹みが出来る原因は、主に半導体本体の硬度や材質とコレットとの相性がミスマッチしていることです。
これを避けるには、製造したい半導体のサイズや薄さ、硬さなどを加味したうえで、適切な材質や形状のコレットを選択していくことが重要になります。
必ずしもこのコレットにすれば安心という最適解はなく、私たちも長年の経験をもとにトライアンドエラーを繰り返して適切なコレットを設計、提供しています。
コレットの交換をすることで得られるメリット
コレットは消耗品で、半導体チップを製造していく過程で段々と望んだ結果を得られなくなっていきます。常に理想のパフォーマンスを発揮させるには、コレットを交換するという作業が必要になってきます。
コレットを交換せずにずっと使い続けることにより、搬送ミスが増えたり、製品の品質に大きな打撃を与える結果となってしまいます。
信用される製品を一定に生み出し続けるためには、ある特定のタイミングで必ずコレットを交換する必要があります。
またサイズ選定も重要で、生産するデバイスに合ったコレットが、装置の本来持っている力を最大限に発揮することでしょう。
コレットの交換頻度を上げる取り組み
コレットを交換することで、常に一定のパフォーマンスを発揮できるとするなら、みなさんは必ず交換しますよね?でもそれが手間だったり、コレットをどのくらい使ったら交換すればよいのか見当がつかなかったりしますよね?
現在ではコレットの交換を効率化する取り組みとして、ダイボンディング装置からコレットを自動的に引き抜いて、新しいコレットを取り付けるという一連の動作を、完全に自動化している機械が存在します。これにより、コレットによるキズや汚れの付着、ダイの表面の損傷や汚染を防止することが出来ます。またコレットのキズや摩耗によるダイボンディング不良の発生を防止できます。
コレットの交換頻度はどのくらいが適切?
自動システムは入れてみたいけれど、そのような予算がない場合、マシーンを容易には導入しなおすことが出来ないという場合は、現在の環境で対応する必要が出てきます。
良質な製品を生み出すための最大のカギとなるのは、コレットの交換のタイミングと頻度です。どういったタイミング、あるいはどのくらいのペースで交換すればよいのかが分かれば、運用はさほど難しくありません。
では、コレットの適切な交換頻度は一体どのくらいなのでしょうか?
交換するためにはまずコレットや製品製造過程を見て人が判断する必要がありますよね。
ここで大切になってくるのが、コレットの状態が悪いとはどういう状態なのかということですよね。
生産が著しくパフォーマンスが落ちたら確かに誰でもわかりますが、そうなる前に見極めたいところです。
コレットを使用していると、搬送時にチップと物理的な接触が伴うため、先端が摩耗して変形してしまいます。
摩耗するコレットを使い続けると、次のような不具合が発生してしまいます。
- デバイスのピックアップができない。
- 搬送中にチップを落下させてしまう。
- プレース時にチップが傾いて、搭載後の姿勢が安定しない。
- コレットからの離れが悪くなり持ち帰ってしまう。
また、一般的に以下のような特徴や環境においては寿命は短くなります。
- 先端や穴径が小さい。
- コレットにかかる圧力や物理的な負荷がある。
- 高温やイオナイザーの雰囲気などコレットが晒されている環境からの負荷が高い。
上記のように使われれ方や使用環境によって大きく寿命が異なり 1万~数百万回と大きく幅があるため、ユーザーが利用状況のデータを取得して独自に交換時期を確認するとよいでしょう。
コレットの提供はオルテへでも行えます
オルテは長年の間、コレットやその他半導体後工程に関連する製造装置の設計、製造に携わってきました。その独自のノウハウを活かして、貴社に合わせた製品を提供することが可能です。
製品の製造は基本的には受注後の手配となっておりますが、弊社で在庫するなどのご相談も承ります、また一定料金以上のご注文で送料無料でお届けしています。オルテに在庫がすでにある製品で対応できる場合においては、数日で納品することも可能です。コレットの他、半導体製造後工程周りの製品では幅広く対応できます。
まとめ
この記事では、半導体製造において必要とされる「コレット」について解説しました。半導体製造器具の先端に取り付けて使用するコレットは、搬送作業に欠かせない重要な部品です。しかし、適切な材質や形状のコレットを選択しなければ、製造過程でキズや汚れ、ダイの表面の損傷や汚染などが発生することがあります。
また、コレットは消耗品であり、半導体の生産効率を最大限に上げつつ、品質を保てるように交換する必要があります。コレットの交換頻度は、コレットの特徴から判別することが出来ます。適切なタイミングで交換することで、コレットが持つ力を最大限に発揮し、良質な製品を生みだします。