スマートフォンからパソコン、家電製品まで、私たちの生活に欠かせない電子機器。その心臓部とも言えるのが、はんだ付け用コネクタです。
小さな部品ですが、その重要性は計り知れません。
本記事では、このはんだ付け用のコネクタの世界に飛び込み、その基本から最新の実装技術まで、わかりやすく解説します。電子機器の製造過程で欠かせないこの技術の魅力に、あなたもきっと引き込まれるはずです。
コネクタの種類と特徴
DIPタイプ(スルーホール実装)
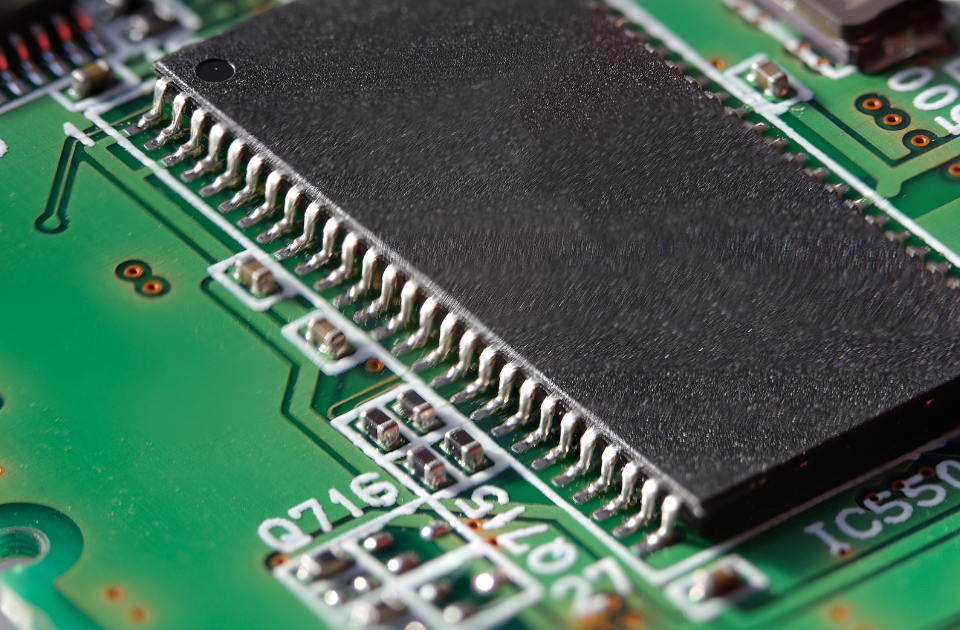
DIP(Dual Inline Package)タイプのコネクタは、基板に穴を開けてリードを差し込むタイプです。
- 基板への取り付け強度が高い
- 小型化や高密度実装が難しい
- 主に手付けやフロー工程ではんだ付けを行う
SMTタイプ(表面実装)
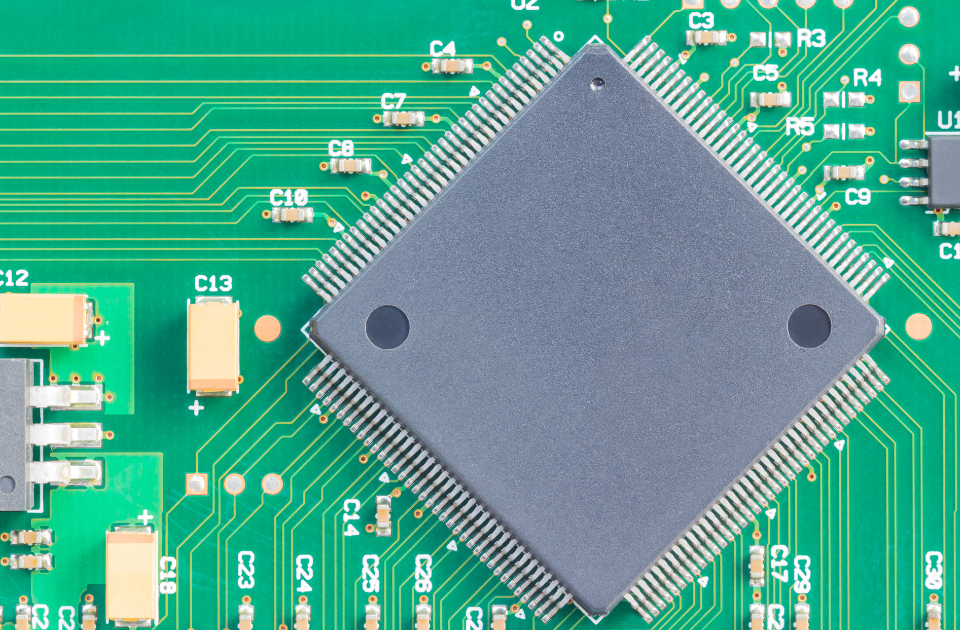
SMT(Surface Mount Technology)タイプは表面実装に適したコネクタで、以下の特徴があります。
- 小型化や高密度実装に適している
- リフロー工程で実装可能
- 基板への取り付け強度は比較的低い
はんだ付けによる実装方法
フロー実装
フロー実装は、溶かしたはんだの槽の上を基板が通過する方式です。
- 部品を搭載した基板の下からはんだを噴き上げる
- DIPタイプのコネクタに適している
リフロー実装
リフロー実装は、クリームはんだを使用する方式です。
- あらかじめクリームはんだを基板に塗布
- 高温の炉を通過させてはんだを溶かす
- SMTタイプのコネクタに適している
はんだ付けによるコネクタ実装時の注意点
コプラナリティ
SMTタイプのコネクタでは、リードの高さの均一性(コプラナリティ)が重要です。不均一な場合、はんだ付け不良の原因となります。
熱による変形
リフロー実装時は、コネクタのプラスチック部品が熱で変形する可能性があります。適切な樹脂材の選択や構造設計が必要です。
特殊な実装方法
ピンインペースト
DIPタイプの利点を活かしつつ、リフロー工程で実装可能な特殊なコネクタです。
- スルーホールリフローやリフローディップとも呼ばれる
- クリームはんだを毛細管現象で吸い上げてはんだ付けを行う
高耐熱コネクタの概要
高耐熱コネクタは、通常のコネクタよりも高い温度環境下で使用できる特殊なコネクタです。一般的なコネクタの耐熱温度が80°C程度であるのに対し、高耐熱コネクタは125°C以上の高温環境下でも使用可能です。
製造方法
高温環境にるコンポーネントには、特殊な材料選定と成形プロセスが必要不可欠です。まず、高耐熱グレードのLCPやPPSなどの樹脂を使用し、金属部品には高温でも特性が変化しにくい特殊合金を採用します。そのため、通常よりも高い温度や圧力での成形が必要となり、さらに高温環境下でも劣化しにくい特殊なめっき処理を施すことが重要です。
これらの対策により、過酷な熱環境下でも安定した性能を発揮できるコンポーネントを実現できます。
製造上の課題
高耐熱コネクタの製造には、材料選定の難しさ、成形技術の複雑さ、品質管理の厳格さ、テストの複雑さといった課題が存在します。
材料は高温下での特性変化が少ないものを選定する必要があり、コストと性能のバランスが求められます。
成形は高温・高圧での加工が必要で、専門的な技術と設備が要求されます。
また、高温環境下での使用を想定するため、より厳密な品質管理が求められます。さらに、性能評価には特殊な試験設備や長時間のテストが必要となります。これらの課題に適切に対応することが、高耐熱コネクタの製造における重要な課題となっています。
コスト要因
高耐熱コネクタの製造コストが高くなる主な要因は以下の通りです。
- 高価な材料耐熱性の高い特殊な樹脂や合金を使用するため、材料コストが上昇します。
- 専門的な製造設備高温・高圧での成形や特殊なめっき処理に対応した設備が必要となります。
- 厳密な品質管理高温環境下での使用を想定した厳格な検査が必要となり、検査コストが増加します。
- 開発コスト高耐熱性能を実現するための材料開発や設計にかかるコストが高くなります。
3Dプリンターで作成されたコネクタの利点は
3Dプリンターは迅速なプロトタイピングが可能で、設計の検証や改良を効率的に行えます。特殊な形状や用途に合わせたカスタムコネクタを金型製作なしで作成できるため、少量生産や特殊用途向けに適しています。コスト削減にもつながり、特に試作段階での効果が期待できます。 3Dプリンターの特性を活かし、従来の製造方法では困難だった複雑な内部構造や形状のコネクタを実現できます。また、設計変更にも迅速に対応できます。 さらに、使用目的に合わせて様々な特性の3Dプリント用材料を選択でき、高品質な表面仕上げも可能です。 一方で、量産や高温環境下での使用など、特定の条件下では従来の製造方法が適している場合もあるため、用途に応じて適切な製造方法を選択することが重要です。
3Dプリンターで作成されたコネクタの価格は
3Dプリンターを活用したコネクタ製造には様々な特徴があります。少量生産では金型不要によるコスト削減が可能ですが、3Dプリント用材料は選ぶ材質によっては高価であり、後処理作業にもコストがかかります。一方、設計の自由度が高まることで、従来の製造方法では困難だった製品の実現が可能となり、コスト削減につながる場合もあります。しかし、高価な3Dプリンター本体の償却コストも考慮する必要があります。製造量に応じて、3Dプリンターと従来の射出成形のどちらが適切かを判断することが重要です。
「3Dプリンティング革命」高耐熱はんだ付け用コネクタの未来
コネクタ製造における高精度と耐熱性の向上は、現代の電子機器製造において非常に重要です。1995年に設立された非公開企業であるZ-Axisは、消費者向けコネクタからミニチュアコネクタまで幅広く対応する技術力を持ち、革新的な製品を提供してきました。しかし、Z-Axisは、通常の3Dプリンティング技術では必要な精度と耐久性を実現できないという課題に直面していました。
Z-Axisが直面した課題とその背景
Z-Axisは、特に±100μmの公差しか達成できなかった従来の3Dプリンティング技術に限界を感じていました。特定の用途において、さらに精密な公差が求められるため、これ以上の精度を必要としていたのです。また、電子機器の高温はんだ付けプロセスに耐えるコネクタの開発が急務となっていました。
microarchを使ったの革新的な3Dプリンティング技術による解決策
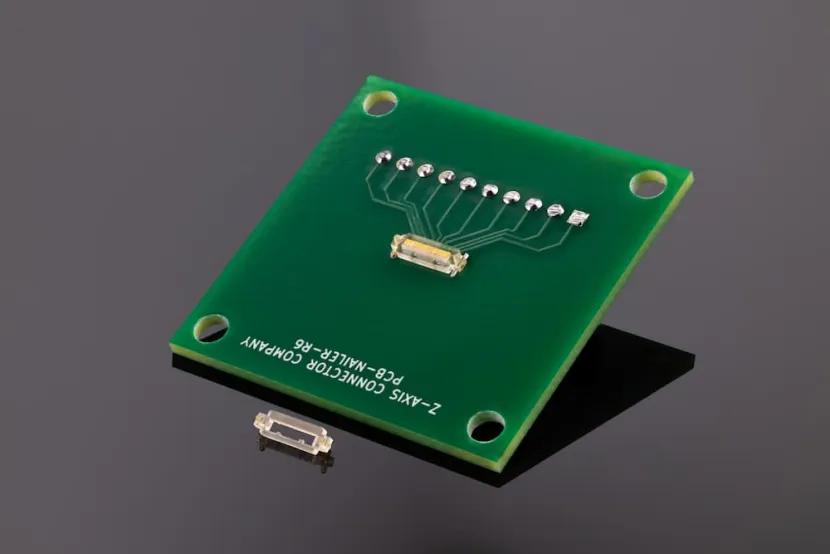
この問題を解決するために、Z-AxisはBMFのマイクロスケール3Dプリンターに注目しました。オルテコーポレーションが代理店を務める、BMF社のPμSL(Projection Micro Stereolithography)技術は、±10~20μmという極めて厳密な公差を達成し、従来の技術では不可能だった小型で高性能なコネクタを実現しました。
さらに、BMFのオープンプラットフォームを活用することで、Z-Axisは3D SystemsのFigure 4® HI TEMP 300-AMB材料を使用し、200°C以上の高温環境下でも安定した性能を維持するコネクタを設計しました。これにより、リフローオーブンでの237°Cの温度に耐えることができ、従来のはんだ付けプロセスにも対応可能です。
コネクタ製造における新たな革新
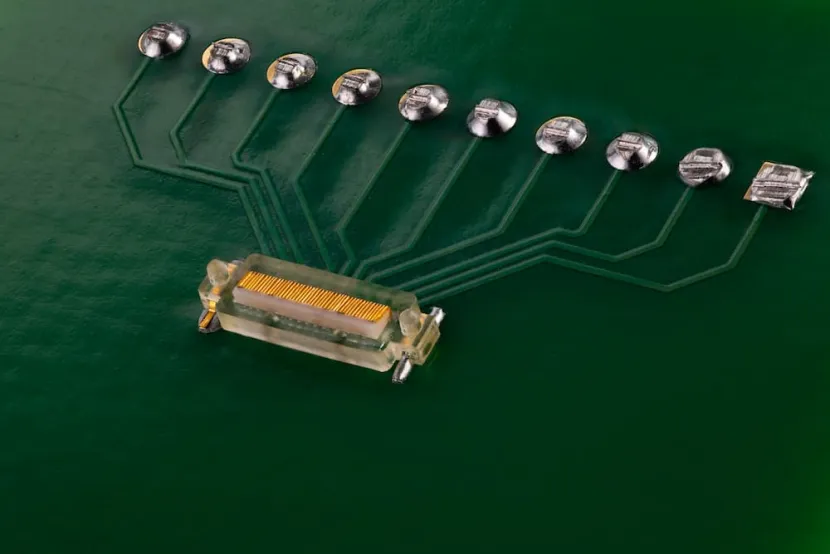
Z-Axisは、BMFの技術を活用することで表面実装部品への移行を実現し、スルーホールの必要がなくなりました。これにより、基板スペースを節約し、製造プロセスの効率を大幅に向上させることができました。電子機器の小型化が進む現代において、この技術は新たな設計の可能性を広げています。
3Dプリンティングがもたらす未来の展望
Z-AxisとBMFの連携により、コネクタ製造の精度と効率は劇的に向上し、従来の製造方法を凌駕する革新的なソリューションが提供されています。この進化により、製造時間の短縮やコスト削減が実現し、業界に新たな基準が確立されました。
まとめ
3Dプリ術の進化、特にBMFのPμSL技術とZ-Axisの専門知識の融合により、高耐熱はんだ付け用コネクタの製造に革命的な変化が起きています。この技術革新は以下の点で業界に大きな影響を及ぼしています。 まず、精度の向上により、従来の技術では不可能だった微細構造の製造が可能になりました。±10~20μmという極めて高い精度を実現したのです。 次に、耐熱性の向上も見られます。200°C以上の高温環境下でも安定した性能を維持するコネクタの製造が可能となり、現代の電子機器製造プロセスに適合しています。 さらに、表面実装部品への移行により、基板スペースの節約と製造プロセスの効率化が実現しました。設計の自由度が高まったのです。 加えて、金型製作が不要になったことで、製造時間の短縮とコスト削減が可能になりました。 この技術革新は、電子機器の小型化と高性能化が進む現代において、コネクタ製造業界に新たな可能性を開きました。今後、この技術がさらに発展し、より広範な用途に適用されることで、電子機器産業全体の発展に大きく貢献することが期待されます。