ワイヤーボンディングは、半導体チップと外部電極を接続するための技術であり、特にトランジスタや集積回路(IC)の電極とプリント基板や半導体パッケージの電極を接続する工程です。この技術は、電力供給や信号の入出力を行うために必要不可欠です。
ワイヤーボンディングの種類
ワイヤーボンディングには主に以下の2種類があります。
ボールボンディング
金線の先端を溶融してボールを形成し、熱・超音波・圧力を用いて基板の電極と接続する方法です。信頼性が高く、広く使用されています。
ウェッジボンディング
ボールを形成せず、金線を直接電極に圧着する方法です。主にアルミワイヤーを使用します。
ワイヤーボンディングの原理
ワイヤーボンディングの基本的なプロセスは以下の通りです。
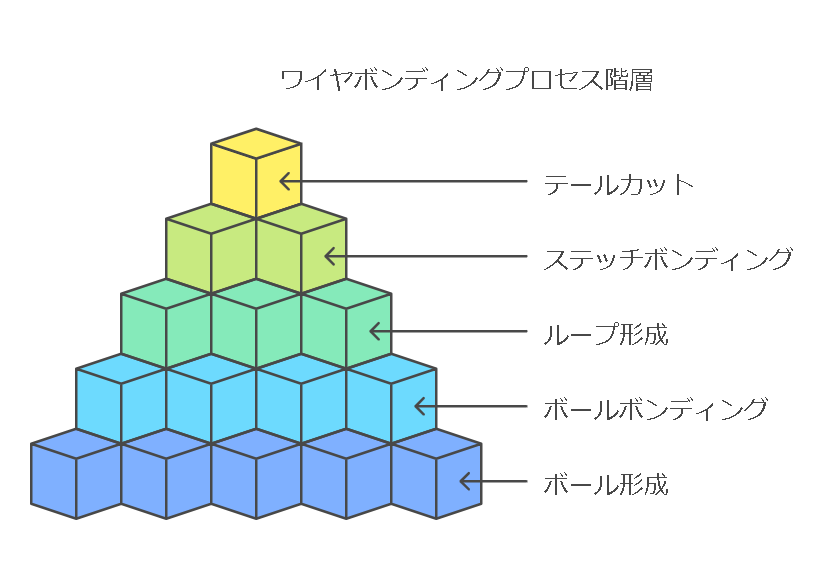
工程 | 説明 |
ボール形成 | ワイヤの先端を放電で溶融し、ボールを形成します。 |
ボールボンディング | 形成したボールをキャピラリで保持しながら電極に押し付け、超音波や熱を加えて接合します。 |
ループ形成 | キャピラリの動きでワイヤに癖を付け、ループの形状や長さをコントロールします。 |
ステッチボンディング | ワイヤを電極に押し付け、接合エネルギーを加えて接合します。 |
テールカット | ワイヤを引き上げて接合端部を切断し、1つのボンディングを完了します |
ワイヤーボンディングの信頼性
ワイヤーボンディングは高温・高圧の条件下で金属間化合物を形成するため、非常に高い信頼性を持ちます。また、金属間化合物の形成により接合強度が高まり、長期間の使用でも安定した性能を維持できます。
ワイヤーボンディングの装置
ワイヤーボンディングを行う装置には、キャピラリと呼ばれる専用ツールが取り付けられています。これにより、ワイヤを正確に電極に接合することができます。
対応ワイヤ径の範囲
ワイヤーボンディングで使用されるワイヤの径は、用途により異なります。一般的には直径10〜100μmの金線や、直径0.1〜0.3mmのアルミワイヤーが使用されます。
ボンディングプロセス
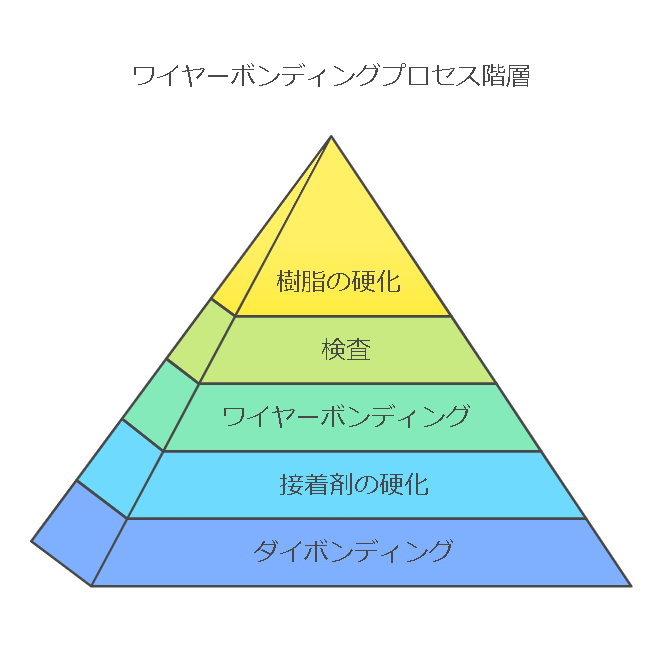
ワイヤーボンディングのプロセスは、以下のステップで行われます。
工程 | 内容 |
ダイボンド | 基板に接着剤を塗布し、ベアチップを搭載します。 |
接着剤の硬化 | オーブンで熱を加え、接着剤を硬化させます。 |
ワイヤーボンド | ワイヤーボンダーで金線を使い、ベアチップと基板パターンを接続します。 |
検査 | 目視検査後、ベアチップとワイヤー部を樹脂封止します。 |
樹脂の硬化 | オーブンで熱を加え、樹脂を硬化させます。 |
受託サービス企業
ワイヤーボンディングを受託サービスとして提供している企業には、WTIやセキアオイテクノなどがあります。これらの企業は、クリーンルームでの作業や高精度なボンディング技術を提供しています。
ボンディングワイヤの種類と材料
ボンディングワイヤには、金、銀、銅、アルミが使用されます。金ワイヤが主流でしたが、最近ではパラジウム被覆銅ワイヤ(PCCワイヤ)や銀ワイヤも使用されています。
金めっきと軟質金
ワイヤーボンディングにおいて、軟質金を使った金めっきは、接合部の信頼性を高めるために重要です。金めっきは、接合部の酸化を防ぎ、接合強度を向上させる役割を果たします。
実装試作
ワイヤーボンディングの実装試作は可能であり、企業によっては試作サービスも提供されています。
超音波併用熱圧着方式
超音波併用熱圧着方式は、熱と超音波を併用してワイヤを電極に接合する方法です。これにより、接合部の強度が向上し、信頼性が高まります。
リペア可能な最小ワイヤ径
ワイヤーボンディングでリペア可能な最小のワイヤ径は、一般的には15μm程度です。
ワイヤーボンディングの映像
ワイヤーボンディングのプロセスを撮影した映像は、企業のウェブサイトや技術紹介ビデオで見ることができます。
最適な金めっき
ワイヤーボンディングに向けた最適な金めっきは、接合部の酸化を防ぎ、接合強度を高めるために重要です。高品質な金めっきは、接合部の信頼性を向上させます。ワイヤーボンディングは、半導体製造において重要な技術であり、その高い信頼性と多様な応用範囲から、広く使用されています。
ワイヤーボンディングの信頼性を高めるためのポイントは何か
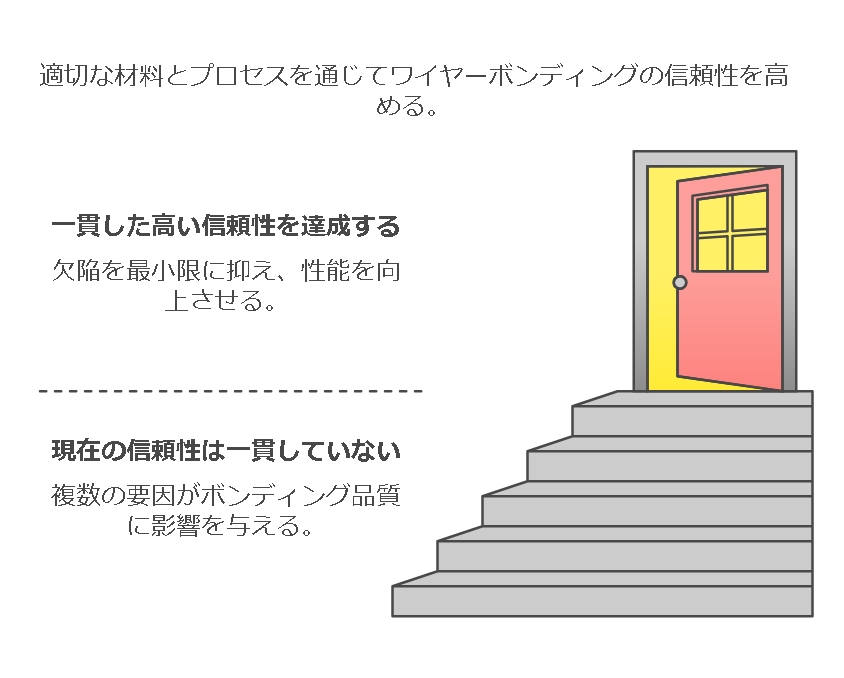
ワイヤーボンディングの信頼性を高めるためには、適切な材料選択、金属間化合物の制御、プロセスの最適化、パッド表面処理、品質管理、信頼性試験の実施、酸化防止対策、工程QCの徹底、スクリーニングの実施、そして継続的な改善が重要です。
具体的には、用途に合わせた適切なワイヤー材料を選択し、ボンディング部での金属間化合物の生成を制御することで接合強度を向上させます。
また、温度、圧力、超音波エネルギーなどのボンディングパラメータを最適化し、安定した接合を実現します。
特に銅ワイヤーを使用する際は、パッド上に緩衝用のメッキ層を設けてチップへのダメージを防ぐ必要があります。
さらに、ワイヤー・プル試験やせん断試験などの破壊検査を定期的に実施し、ボンディング品質を確認するとともに、高温放置試験などの加速評価試験を行って長期的な信頼性を予測します。
製造工程における品質管理を徹底し、不良の発生を最小限に抑えるためのスクリーニング検査の実施も重要です。
最後に、市場実績の解析や信頼性試験の結果を基に、弱点を特定し、改善および再発防止策を講じることで、継続的な品質向上が可能となります。
ワイヤーボンディングの信頼性向上に最も効果的な方法は何か
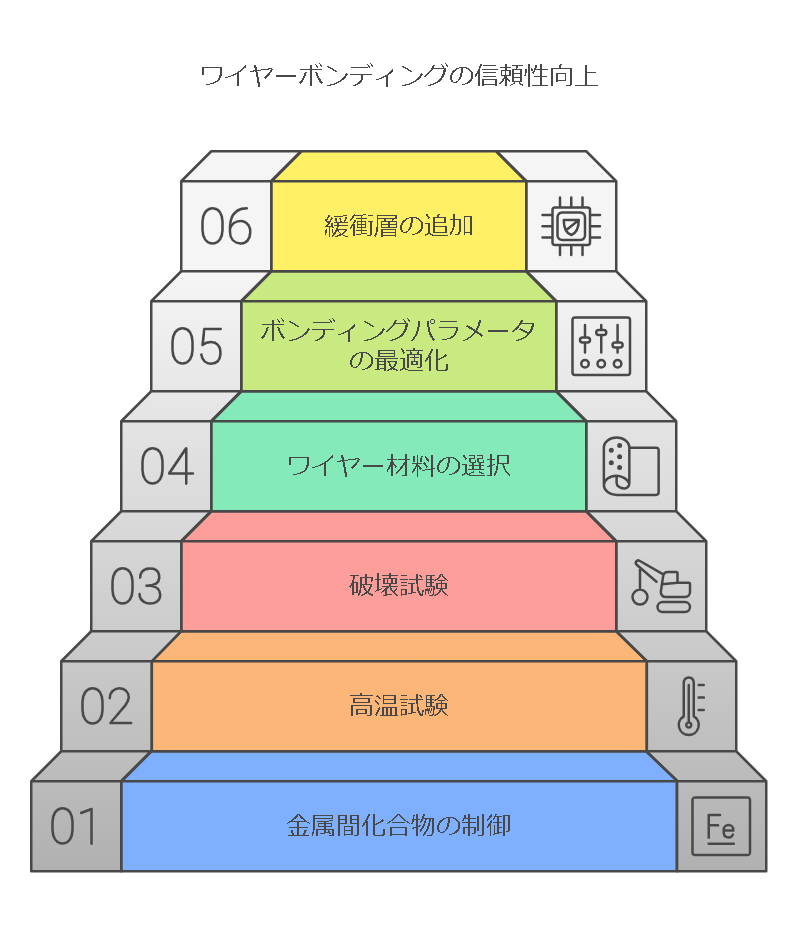
まず、金属間化合物の適切な制御が重要です。ボールボンディング部の接合強度は金属間化合物の生成によって増加しますが、過剰な生成は信頼性を低下させる可能性があるため、適切な量と種類の金属間化合物を形成することが重要です。
次に、長時間の高温放置試験(1000〜2000時間、100〜250℃)を実施し、接合部の耐久性を確認することで、金属間化合物の成長とそれに伴う信頼性の低下を予測し、対策を講じることができます。
また、ワイヤー・プル試験やせん断試験などの破壊検査を定期的に実施し、接合部の強度と品質を評価することで、製造工程での不良を早期に発見し、改善策を講じることができます。
さらに、使用するワイヤーの材料(金、銅、アルミニウムなど)を適切に選択し、各材料の特性に応じたプロセスパラメータを設定することが重要です。特に銅ワイヤーの場合、酸化防止対策が必要です。
加えて、温度、圧力、超音波エネルギーなどのボンディングパラメータを最適化し、安定した接合を実現することで、接合部の信頼性を向上させることができます。
最後に、特に銅ワイヤーを使用する場合、パッド上に緩衝用のメッキ層(Ni+Cu+Pgなど)を設けることで、チップへのダメージを防ぐことができます。
これらの方法を適切に組み合わせ、管理することで、ワイヤーボンディングの信頼性を大幅に向上させることができます。
まとめ
ワイヤーボンディングは、半導体製造において不可欠な技術であり、その信頼性と精度が製品の品質に直結します。適切な材料選択、プロセスの最適化、品質管理の徹底などを通じて、ワイヤーボンディングの信頼性を高めることが重要です。継続的な改善と最新技術の導入により、さらに高い性能と信頼性を追求することができるでしょう。