3D造形を活用してPDMS成型用のマスター型を造ることにより、PDMSデバイスの作成時間とコストは大きくカットできます。さらに造形に余分なプリント時間を減らしリードタイムを短縮することは、大きなメリットです。microArch ®プリンターを使用すると、コスト削減と時間削減の二つの観点からほかの加法プロセスと比較してさらに時間を短縮することができます。
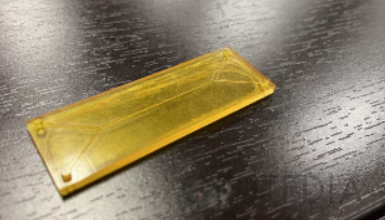
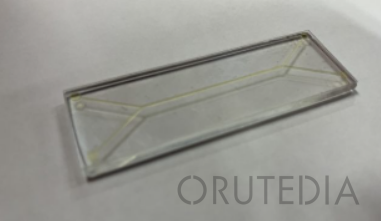
基盤への印刷
ガラス基盤の上面にプリントすることで造形時間を短縮し、microArchシステムは、高解像度とディテールが重要な流路パターン部分の造形のみを行うことができます。プリントに使用される基板は、一般的な顕微鏡のスライドガラスです。
ガラス基板は、小さな部品を印刷するには優れたベースですが、プリントされた部品とガラスとの接着力は、PDMS成形アプリケーションにとって十分な強度がありません。基板上の機能が剥離に耐えられるよう、十分な接着力が必要です。そこで提案方法では最上面に透明なビニールシートをガラス基板に付着させることで問題を解決しました。このプロセスは費用対効果が高く、準備にかかる時間はわずか数分です。
PDMS成形用のこのマイクロ流体デバイスマスターパターンは、4mmの基礎部分の上に400µmのチャネルを持っています。従来の方法ではマスターパターンの基礎部分を含む全体を印刷するため4~5時間程度かかります。
今回の提案方法では、3mmのスライドガラスと1mmのRinzyl製使い捨てスライドガラスの位置をそろえて接着することで、4mm厚の基礎部分を印刷する必要をなくしました。
このように印刷前に組み立て式の土台をプラットフォームに追加すると、印刷に必要なのはマイクロチャネルのみで、印刷に30分しかかかりません。
マスターパターンのテスト
ガラス基板への流路パターンの密着性は、セロハンテープを上面に貼って剥がすテストしました。テープを剥がす作業を数回繰り返した後、基板からのパターンが剥がれることはありませんでした。
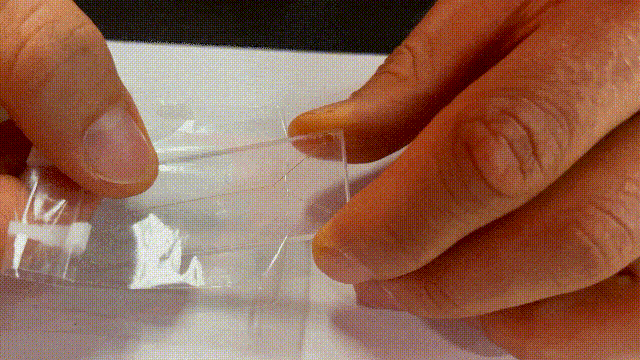